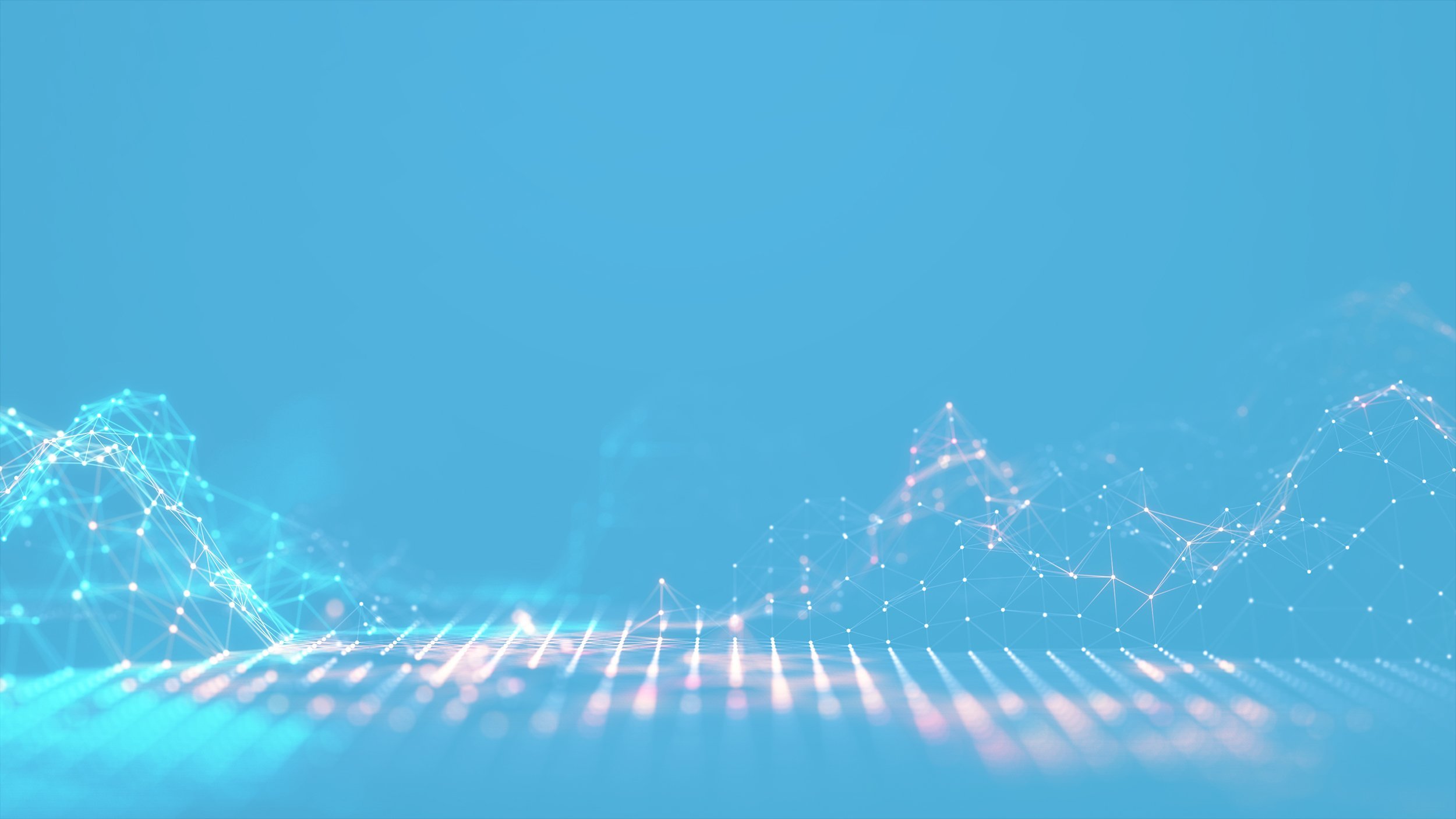
Drive growth by integrating new technologies
Improve organizational performance
Tackle labor shortages
Process Optimization
Digital
Transformation
Identify and Eliminate Common Business Inefficiencies
In many organizations, key processes often take a significant amount of time and resources to complete. This can lead to inefficiencies, delays, and employee overload.
Inefficiencies Regularly Identified by ARIV Include:
Lack of integration between systems
✶
Redundant data entry
✶
Repetitive manual tasks
✶
Paper overuse
✶
Lack of integration between systems ✶ Redundant data entry ✶ Repetitive manual tasks ✶ Paper overuse ✶
Repetitive manual tasks; Can lead to human error and wasted time
Redundant data entry; The same data is entered multiple times into different systems
Lack of integration between systems; Applications or software that do not communicate with each other, forcing staff to manually transfer information from one system to another
Paper overuse; Excessive reliance on paper documents slows down processes, increases storage costs, and increases document management costs.
This approach not only ensures better operational performance, but also successful adaptation to technological change.
Through a detailed mapping of current processes, we identify inefficiencies and areas for improvement. This enables us to rethink and reengineer processes to make them more efficient, reduce costs, and maximize the use of new technologies. This approach ensures not only better operational performance, but also successful adaptation to technological change.
Furthermore, with the arrival of new software and technologies, it is crucial to reassess and adapt existing processes to ensure they are aligned with the capabilities and benefits offered by these innovations.
Using a process optimization service can help overcome these challenges. By carrying out a detailed mapping of current processes, we identify inefficiencies and areas for improvement. This enables us to rethink and re-engineer processes to make them more efficient, reduce costs and maximize the use of new technologies.
Overcoming Operational Challenges with Process Engineering: the Opportunities
When a company realizes that its processes are not optimal, it must aim to increase the speed of its operations, reduce the number of people involved and improve overall fluidity.
Major investments in technology or new processes also require rigorous deployment planning to avoid additional costs. This includes quickly configuring processes and related solutions, as well as managing the immediate impact on people, materials and equipment in use. The goal of this plan is to optimize the investment from the outset.
Several Opportunities Arise from Process Optimization:
There are also critical processes that require optimization. An example of a critical process is manufacturing, from raw material procurement to final assembly. If poorly coordinated, delays and bottlenecks can occur.
A proactive approach to reengineering these critical processes ensures that operations remain smooth and efficient, minimizing risk and maximizing quality.
To learn more about available grants, please contact us by filling out the form in the link below.
What Does Process Optimization Look Like?
During the digital audit, the team at ARIV will have created one or more detailed maps of current processes. To develop an effective process improvement strategy, the team will first deepen its understanding of critical and complex processes, and then analyze those with less impact on operations.
Here are the steps we'll take together:
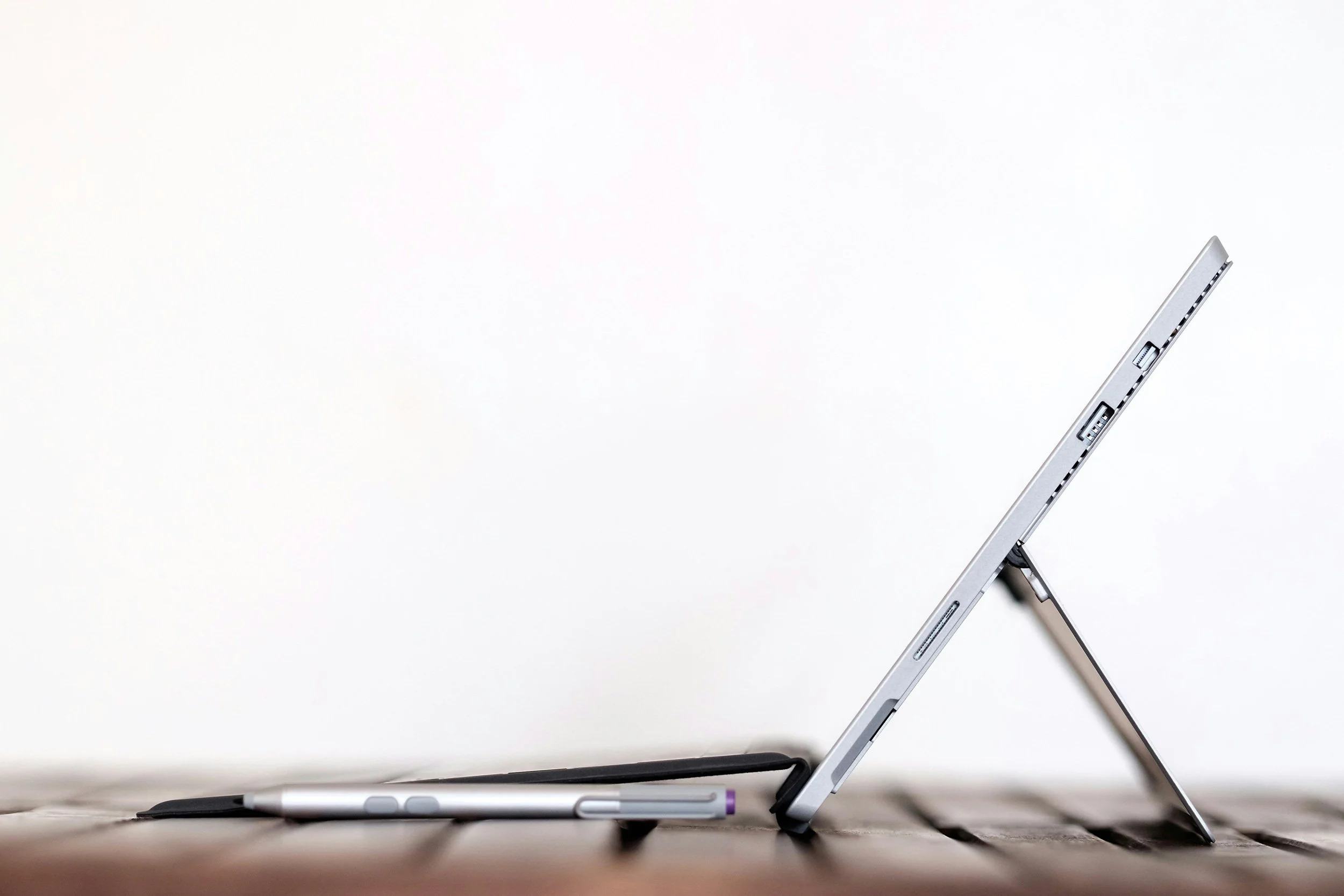
Context and Basis of Our Recommendations
Once we have completed the mapping of current processes, we offer you a fresh look at the changes required. These may include partial or complete automation of certain steps in your company's existing processes.
Our process reengineering recommendations include:
Redistribution of responsibilities
Automating of selected tasks for different process participants
Improving workflows
Integrating decision support tools into the process
Suggesting performance indicators to measure change
Expected Results from Process Redesign
The greatest benefit to the company performing process reengineering is improved operational efficiency. You'll quickly see a reduction in project cycle times or production lead times.
The company will benefit from a significant reduction in operating costs. Employees who were previously engaged in manual tasks or redundant data entry can be reassigned to value-added tasks, reducing administrative costs. Work processes will be optimized, and administrative effort reduced, resulting in an overall increase in productivity.
Improve customer satisfaction by providing faster responses and meeting customer needs in less time, resulting in better overall experience. An improved work environment with smoother processes and fewer repetitive tasks will have a positive impact on employee satisfaction.
By partnering with ARIV, you ensure the successful implementation of new processes within your organization. What's more, process optimization is an excellent input for change management.
Improved operational efficiency (reduced project cycle times or production lead times)
Significant reduction in operational costs
Increased productivity through streamlined operations and reduced administrative overhead
Improved overall customer experience through more efficient and faster response